In today's rapidly evolving electric vehicle (EV) market, standing out among numerous models is no easy task. A high-performance electric car relies heavily on a robust and reliable Battery Management System (BMS). To build an advanced BMS, it's crucial to incorporate isolated power supplies and isolated CAN transceivers. But how do you choose the right isolation solutions for your BMS design?
**First, understanding the role of BMS in electric vehicles**
The Battery Management System (BMS) acts as a critical link between the vehicle's battery pack and the overall system. Its primary functions include real-time monitoring of battery parameters such as voltage, current, and temperature; evaluating battery health; performing diagnostics and issuing alarms; and managing battery balancing.
Electric vehicle batteries are typically composed of multiple cells connected in series and parallel to achieve higher power and energy capacity. However, due to manufacturing limitations, individual cells may vary in performance, leading to imbalances and potential safety risks. This is where the BMS becomes essential—it ensures efficient and safe management of the entire battery pack.
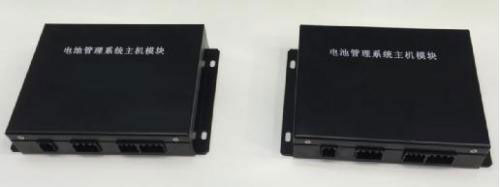
**Second, how does the BMS work?**
The BMS works closely with the vehicle’s power battery to monitor and manage its performance. It continuously collects data from sensors to track battery conditions, such as voltage, current, and temperature. It also manages battery state, performs leakage detection, thermal management, and battery balance control. Additionally, it calculates key metrics like State of Charge (SOC), State of Health (SOH), and discharge power.
All this data is transmitted through the CAN bus interface to various systems, including the vehicle master controller, motor controller, and energy control system. This real-time communication ensures effective and safe battery management. The system architecture is illustrated in Figure 2.
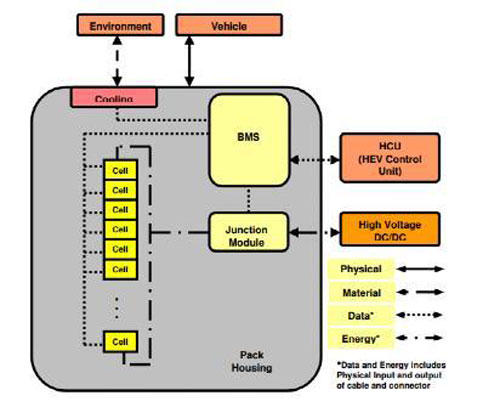
**Third, the three essential elements of a BMS**
To ensure the BMS operates reliably, three key factors must be considered:
1. **Isolated Power Supply**: With multiple BMS modules in a vehicle, each drawing power from the same battery, it's important to isolate them to prevent interference. An isolated DC-DC power supply at the input stage helps maintain module independence and stability.
2. **Isolated CAN Communication**: The internal communication environment in a vehicle can be noisy, with surges and pulses that could disrupt data transmission. Isolating the CAN interface protects against these issues and improves signal integrity.
3. **High-Level Power Isolation**: Since EV battery packs often operate at voltages up to 500 VDC, it's vital to protect the low-voltage side of the system. Isolated DC-DC converters are commonly used to separate high and low voltage sides, ensuring driver and system safety.
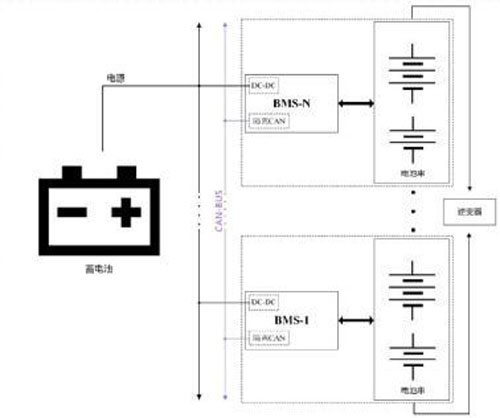
**Fourth, recommended isolation solutions for BMS**
For security and reliability, BMS systems require both power and signal isolation. Typically, a 12V or 24V power supply is used, with isolated DC-DC modules ranging from 2W to 6W depending on the application. For high EMI environments, adding a π-type filter circuit at the input of the isolated DC-DC module can further enhance performance.
When it comes to CAN communication, isolation and anti-interference measures are crucial. Designers should focus on protecting the communication interface to ensure reliable and secure data exchange between the BMS and other vehicle systems.
By implementing these isolation strategies, manufacturers can build more robust, safe, and efficient BMS solutions that meet the growing demands of the electric vehicle industry.
Industrial Computer
An industrial computer is a specialized computing device designed to operate in harsh industrial environments. These computers are built to withstand extreme temperatures, dust, moisture, vibrations, and other challenging conditions that would damage or render a standard desktop computer inoperable.
Mini
Industrial PC is designed to provide reliable and high-performance computing for industrial applications. They often feature powerful processors, such as Intel Core i-series or AMD Ryzen processors, and can have large amounts of memory and storage to handle complex tasks.
In addition to standard computing features, industrial computers may also have specialized features such as multiple serial ports, Ethernet ports, and digital I/O ports for connecting to industrial equipment and sensors. Some industrial computers also support wireless connectivity options such as Wi-Fi and Bluetooth.
In conclusion, Embedded Industrial PC is specialized computing devices that are designed to operate in harsh industrial environments. They offer reliable and high-performance computing for a wide range of industrial applications, and their durability, customization options, and long lifecycle make them an ideal choice for industrial users.
Mini Industrial Pc,Industrial Mini Pc,Fanless Indutrial Pc,Industrial Computer,Embedded Industrial PC
Shenzhen Innovative Cloud Computer Co., Ltd. , https://www.xcypc.com