Abstract : Ceramic substrate materials are widely used in power electronics, electronic packaging, hybrid microelectronics and multi-chip modules due to their excellent thermal conductivity and air tightness. This paper briefly introduces the current status and future development of ceramic substrates.
1 Comparison of plastic and ceramic materials Plastics, especially epoxy resins, still dominate the entire electronics market due to their relatively good economics, but many special fields such as high temperature, coefficient of linear expansion, mismatch, air tightness, stability, and mechanical properties are obvious. Not suitable, even if a large amount of organic bromide is added to the epoxy resin, it does not help.
Compared with plastic materials, ceramic materials play an important role in the electronics industry. They have high electrical resistance, high frequency characteristics, high thermal conductivity, good chemical stability, high thermal stability and high melting point. These properties are highly desirable in the design and manufacture of electronic circuits, so ceramics are widely used for substrate materials of different thick films, films and circuits, and can also be used as insulators for conducting thermal paths in thermally demanding circuits and for Manufacturing various electronic components.
2 Comparison of various ceramic materials 2.1 Al2O3 So far, alumina substrates are the most commonly used substrate materials in the electronics industry because of their high mechanical and thermal properties, high strength and chemical stability relative to most other oxide ceramics, and abundant raw material sources. A variety of technical manufacturing and different shapes.
2.2 BeO It has a higher thermal conductivity than metal aluminum and is used in applications requiring high thermal conductivity, but it rapidly decreases after the temperature exceeds 300 °C.
The most important thing is that its toxicity limits its development.
2.3 AlN AlN has two very important properties worth noting: one is a high thermal conductivity and the other is a coefficient of expansion that matches Si. The disadvantage is that even a very thin oxide layer on the surface has an effect on the thermal conductivity. Only a strict control of the material and process can produce a uniform ARN substrate. At present, the large-scale production technology of AlN is still immature in China. Compared with Al2O3, the price of AlN is relatively high, which is also a bottleneck restricting its development.
Based on the above reasons, it can be known that alumina ceramics are widely used in the fields of microelectronics, power electronics, hybrid microelectronics, and power modules due to their superior comprehensive performance.
3 Ceramic substrate manufacturing It is very difficult to manufacture high-purity ceramic substrates. Most ceramics have high melting point and hardness, which limits the possibility of ceramic machining. Therefore, ceramic substrates are often doped with lower melting point glass for fluxing or bonding. The final product is easy to machine. Al2O3, BeO, AlN substrate preparation process is very similar, the base material is ground to a powder diameter of about several microns, mixed with different glass flux and adhesive (including powdered MgO, CaO), in addition to the mixture Some organic binders and different plasticizers are ball milled to prevent agglomeration to make the ingredients uniform, to shape the green sheets, and finally to high temperature sintering. At present, ceramic molding has the following main methods:
Roller Rolling The slurry is sprayed onto a flat surface, partially dried to form a sheet of viscous like putty, and the sheet is fed into a pair of large parallel rolls to obtain a uniform thickness of the green sheet.
• Casting The slurry is applied to a moving belt to form a sheet by a sharp blade. This is a low pressure process compared to other processes.
• Powder compaction The powder is sintered in a hard mold cavity and subjected to a large pressure (about 138 MPa). Although the pressure unevenness may cause excessive warpage, the sintered part produced by this process is very dense and has a small tolerance.
â— Isostatic powder compacting This process uses a mold that is surrounded by water or glycerin and uses a pressure of up to 69 MPa to produce a more uniform warpage of the parts.
Extrusion Slurry is extruded through a die. The process used in this process has a low viscosity and it is difficult to obtain a small tolerance, but this process is very economical and can obtain thinner parts than other methods.
The author of this article is Taiwan 奕锜 / Shenzhen Hong Chuangxing Wang Gang
Piezoelectric ceramic disc
Quick delivery
High performance
Application: flow meter measurement
There are many kinds of USF used in closed pipeline according to the measuring principle, and the most commonly used are propagation time method and Doppler method. Among them, time difference ultrasonic flowmeter is used to measure fluid flow by the principle that the time difference of sound wave propagating downstream and countercurrent is proportional to the velocity of fluid flow. It is widely used in raw water measurement of rivers, rivers and reservoirs, process flow detection of petrochemical products, water consumption measurement of production process and other fields. According to practical application, time-difference ultrasonic flowmeter can be divided into portable time-difference ultrasonic flowmeter, fixed time-difference ultrasonic flowmeter and time-difference gas ultrasonic flowmeter.
Ultrasonic flow-meters use at least two transducers aligned so that ultrasonic pulses travel across the flow of liquid or gas in a pipe at a known angle to the flow.
Technical data:
Electromechanical coupling coefficient Kp: > 0.62
Dielectric Loss tg δ: <2%
Nominal Piezo discs for ultrasonic flowmeter:
OD14.2*1MHz PZT-51
OD14.6*1MHz PZT-51
OD15*1MHz PSnN-5
OD15*2MHz PSnN-5
OD20*1MHz PSnN-5
OD20*2MHz PSnN-5
OD15*1MHz PZT-51
OD15*2MHz PZT-51
OD20*1MHz PZT-51
OD20*2MHz PZT-51
Size, Frequency and Electrode on request.
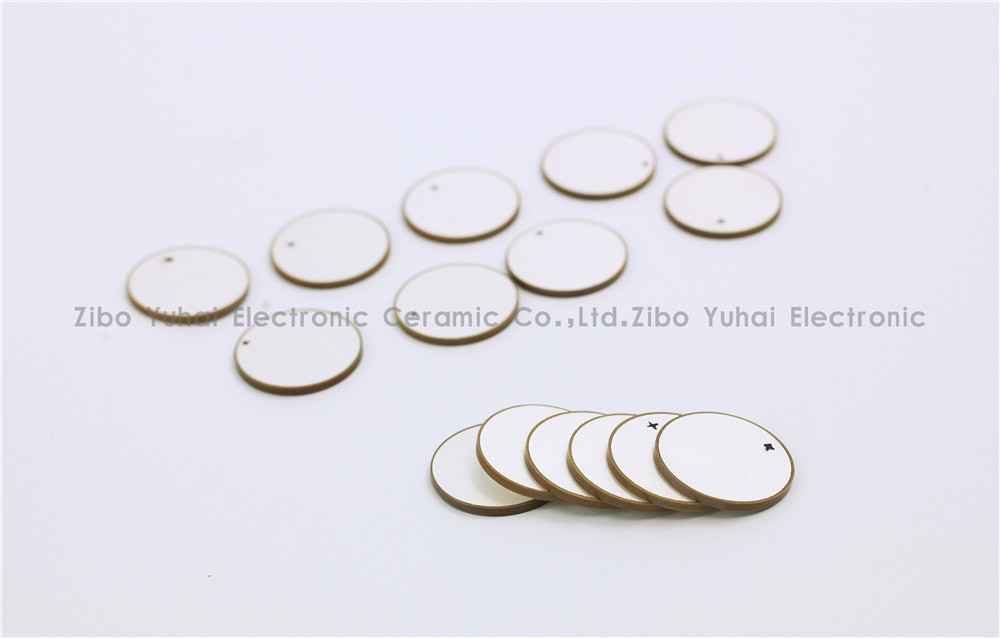
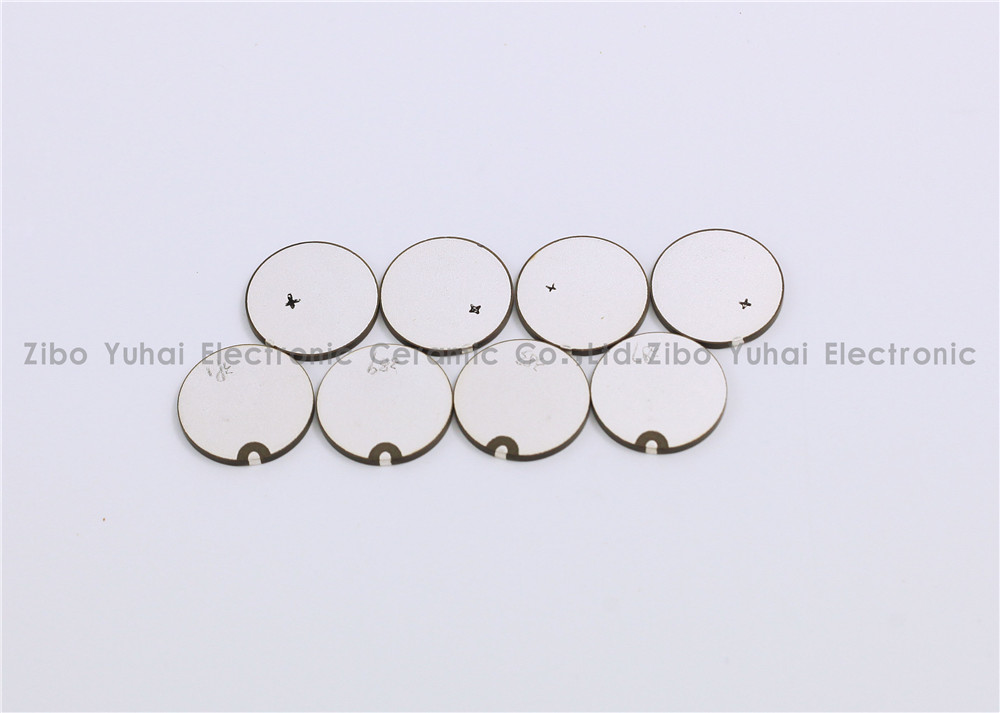
Piezoelectric Discs For Flowmeter Sensor
Piezoelectric Ceramic Disc,Piezoelectric Discs For Flowmeter Sensor
Zibo Yuhai Electronic Ceramic Co., Ltd. , https://www.yhpiezo.com